Students have represented Georgia Tech in maritime robotics competitions since as early as 2005. The Marine Robotics Group in its current form started in 2016.
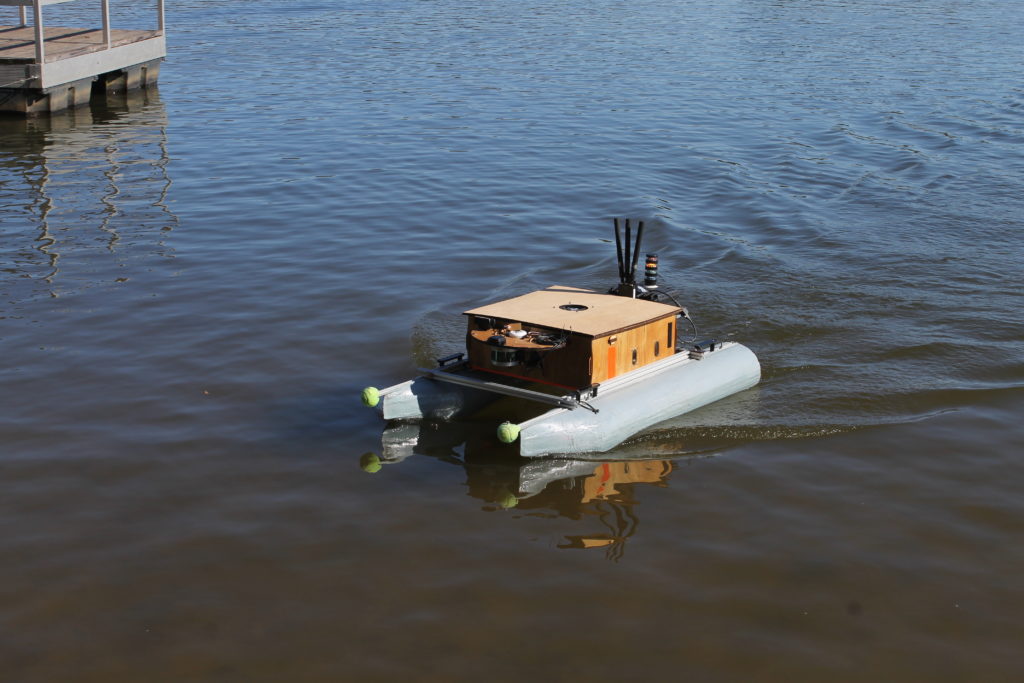
Vinny (2017-2019)
This modular pontoon boat competed in RoboBoat competitions in 2017, 2018, and 2019. It was refit with a new pair of fiberglass pontoons for the 2018 competition. It was further refit with lighter LiPo batteries replacing the heavy Torqeedo battery for 2019. The design is modular and allows for easy modification.
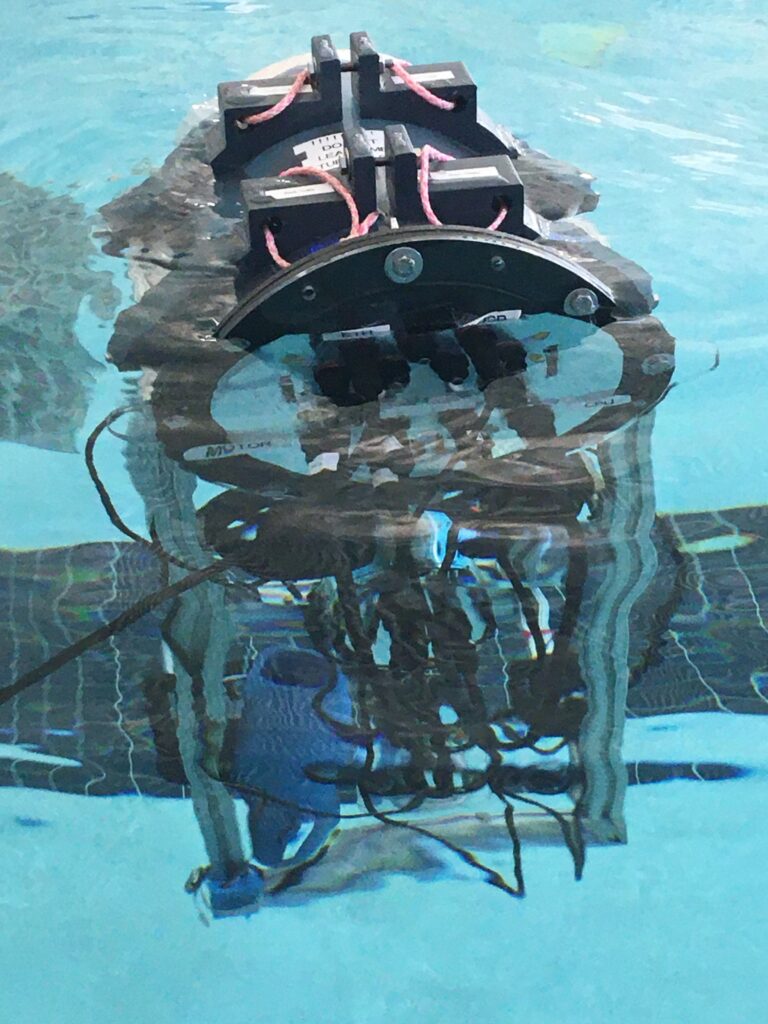
Plongeur (2017-2019)
This autonomous submersible competed in RoboSub 2017, 2018, and 2019. It features an accessible electronics housing, and has high roll and pitch stability.
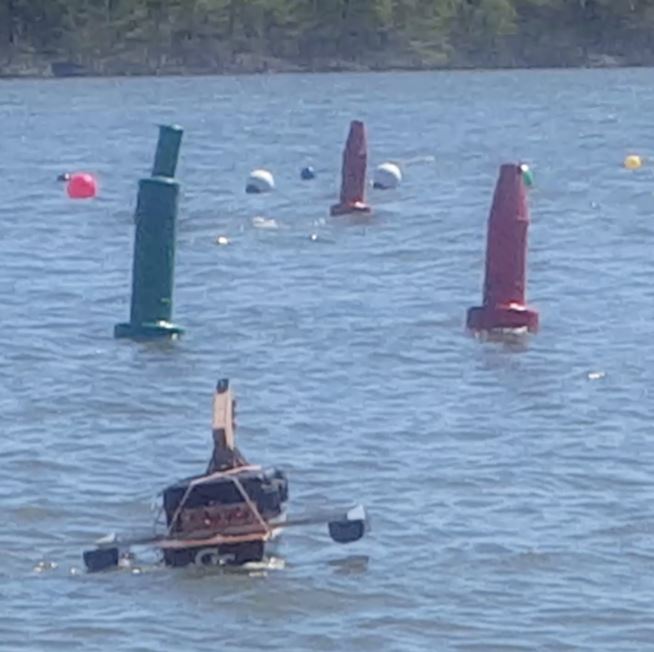
Burnadette (2016)
This trimaran is the rebirth of Captain Hindsight. Burnadette was outfitted with LIDAR and featured a simulation-based approach.
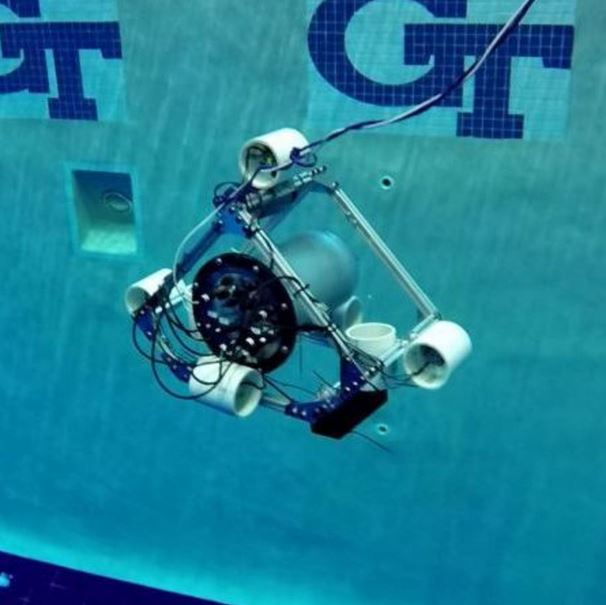
Suby McSubface (2016)
This autonomous underwater vehicle competed in RoboSub 2016.
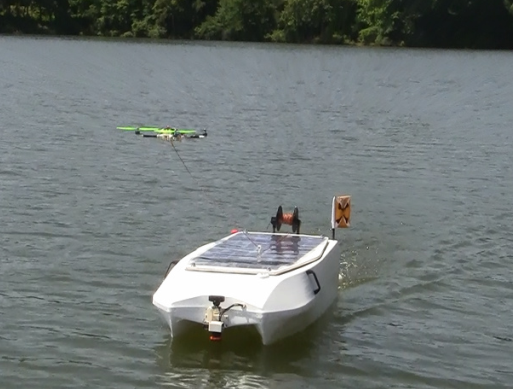
Leucothea (2015)
This boat featured a large vacuum-formed plastic hull, waterjets, and a tethered quadcopter. It competed in RoboBoat 2015.
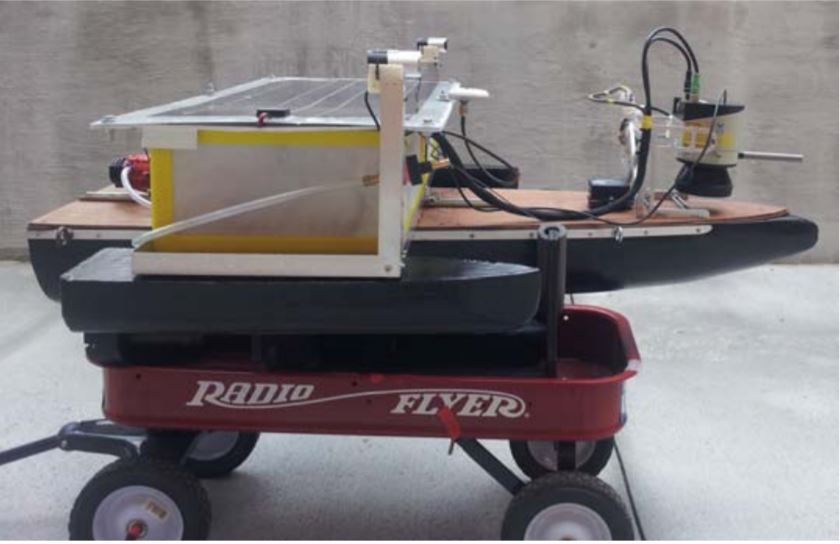
Captain Hindsight (2012, 2014)
This boat competed in Roboboat 2012 and 2014. It featured a trimaran design with various stability improvements made following Captain Planet.
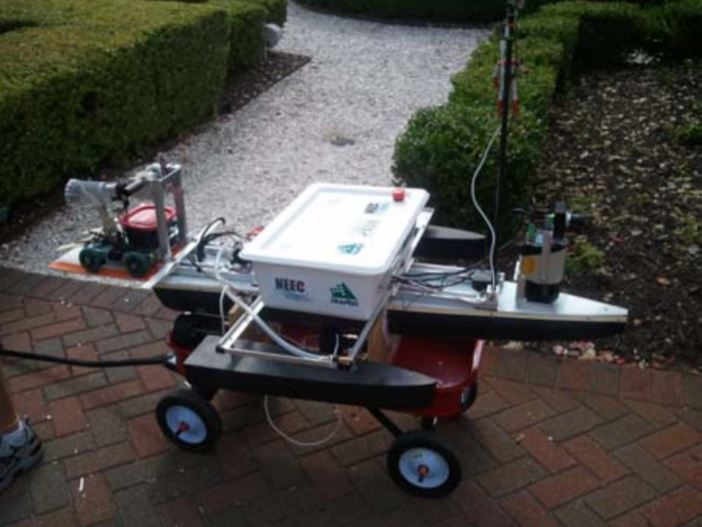
Captain Planet (2011)
This boat competed in RoboBoat 2011 and featured a trimaran design.
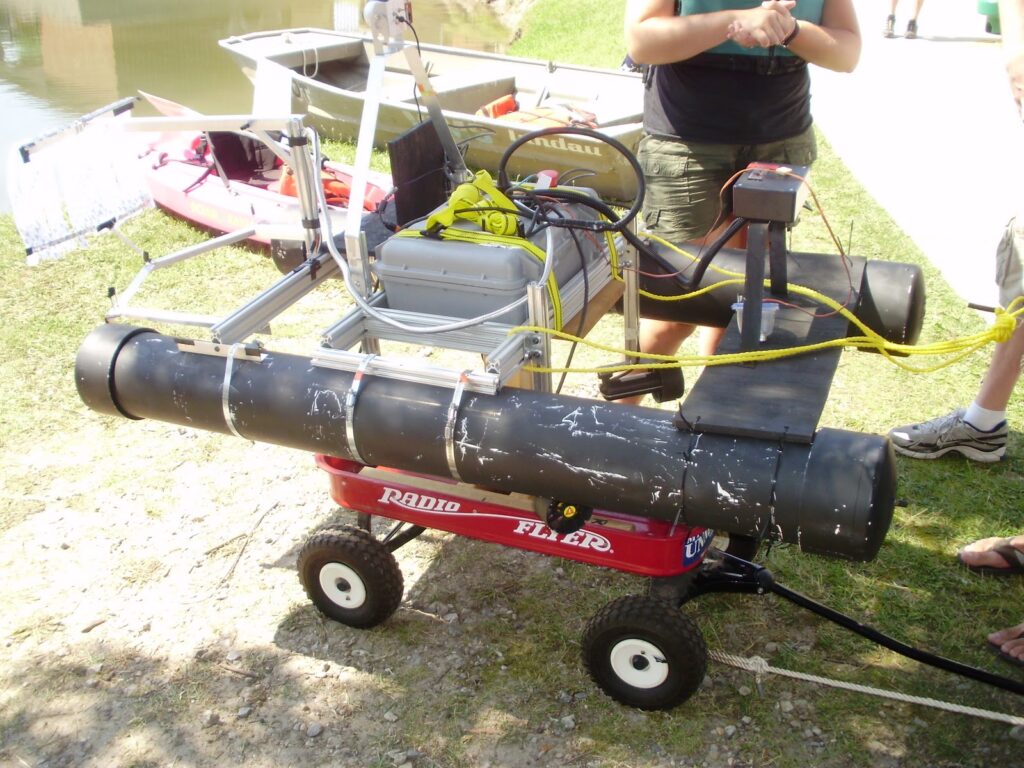
GT Baggins (2010)
Georgia Tech’s entry to the 3rd Annual AUVSI and ONR Autonomous Surface Vehicle Competitions was designed following three core principles: (1) modularity, (2) robustness, and (3) cost-effectiveness. Much of the hardware was recycled from prior underwater vehicles, allowing for a cost-effective solution. The catamaran design’s hulls were built by sealing two 6in in diameter and 5ft in length PVC pipes. The structure was comprised of 80/20® aluminum pieces allowing for maximum modularity and flexibility. This design allowed the team to place amongst the middle tier of the competition for a fraction of the material cost of all the other teams.
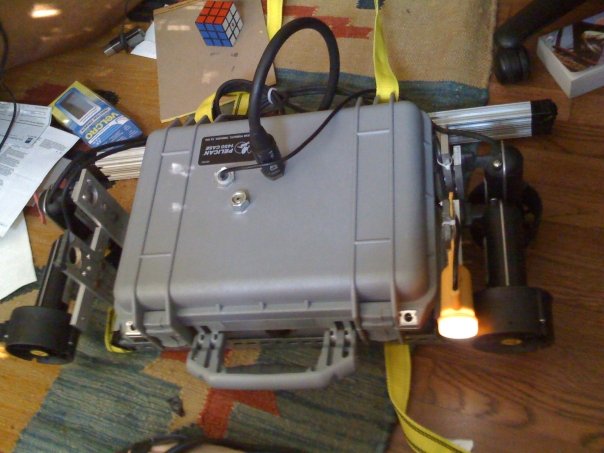
Subby Jr. (2008)
Georgia Tech’s entry to the 11th annual AUVSI and ONR Autonomous Underwater Vehicle Competition was a complete redesign of the vehicle. The hull was a waterproof PelicanTM case attached to a 80/20® aluminum frame. Four seabotix thrusters were attached to the frame. This design fixed many of the problems presented by the old hull, namely, it produced a simpler, and more modular and accessible design. A new smaller and more powerful computer made the design not only more elegant, but more capable as well. Subby Jr. also incorporated a new sensor suite comprised of new depth and tilt sensors, inertial measurement unit, and a new waterproof camera.
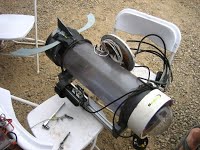
Subby II (2007)
Georgia Tech’s entry to the 10th annual AUVSI and ONR Autonomous Underwater Vehicle Competition was an updated version of the 2006 and 2007 models. The main hardware updates were the addition of a digital compass and gyro to improve the ASV’s navigation capabilities. In terms of software, Subby II was GT MRG’s first Windows XP operated AUV, all prior designs used Linux as their operating system. In terms of hull design, Subby II was identical to Subby I except for the addtion of the fins shown in the picture. The fins were added during competition to improve the vehicle’s underwater tracking abilities.
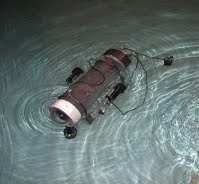
Subby I (2006)
Georgia Tech’s entry to the 9th annual AUVSI and ONR Autonomous Underwater Vehicle Competition. Subby was an evolutionary development from The Mongoose design and leverage much of its hardware and electronics. This allowed the team to focus its efforts in improving the AUV’s performance rather than conceiving, constructing and testing a completely new design. The major improvements done on Subby I included a new dome end cap for the hull to allow better vision underwater, and four new seabotix thrusters.
The Mongoose (2005)
Georgia Tech’s first entry to the Annual AUVSI and ONR Autonomous Underwater Vehicle Competition was developed around simple, cost effective solutions to the challenges presented in the competition. The Mongoose included a single watertight chamber of clear PVC. Attached to this PVC tube was an aluminum frame used to mount motors and instruments. Propulsion was provided by four trolling motors, controlling translation and rotation about two axes. Stability about the third axis (roll) is maintained by locating the center of gravity below the center of buoyancy.